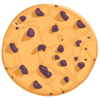
We use cookies to offer you the best experience on our site. You can find out more about the cookies we use or disable them in the Cookie settings
Single-use devices are deeply rooted in the life science, pharmaceutical, diagnostic, and medical industries. The use of plastics for prototyping and serial manufacturing in these sectors is critical, due to the highest standards of precision, cleanliness, and functional integrity.
Such tight tolerances and purity levels are achievable through precision clean injection molding in ISO-certified clean environments. To maintain the cleanliness chain, devices are often delivered as “ready-to-use,” fully assembled, packed, and sterilized.
Since 2002, Aseptic Technologies has pioneered the design, clean injection molding, and sterilization of pharmaceutical-grade products including the AT‑Closed Vial®, disposable aseptic connectors, and others.
Sterility by Design
Each part is molded in cleanroom conditions—up to ISO 5—and delivered ready for sterilization, maintaining lowest bioburden from start to finish.
End-to-End Control
In-house mold design, validation, production, assembly, packaging, and documentation guarantee process integrity, traceability, and regulatory readiness.
Scalable & Compliant
From small-scale prototyping to full industrial production, our solutions align with tight regulatory standards and evolving biotech innovation needs.